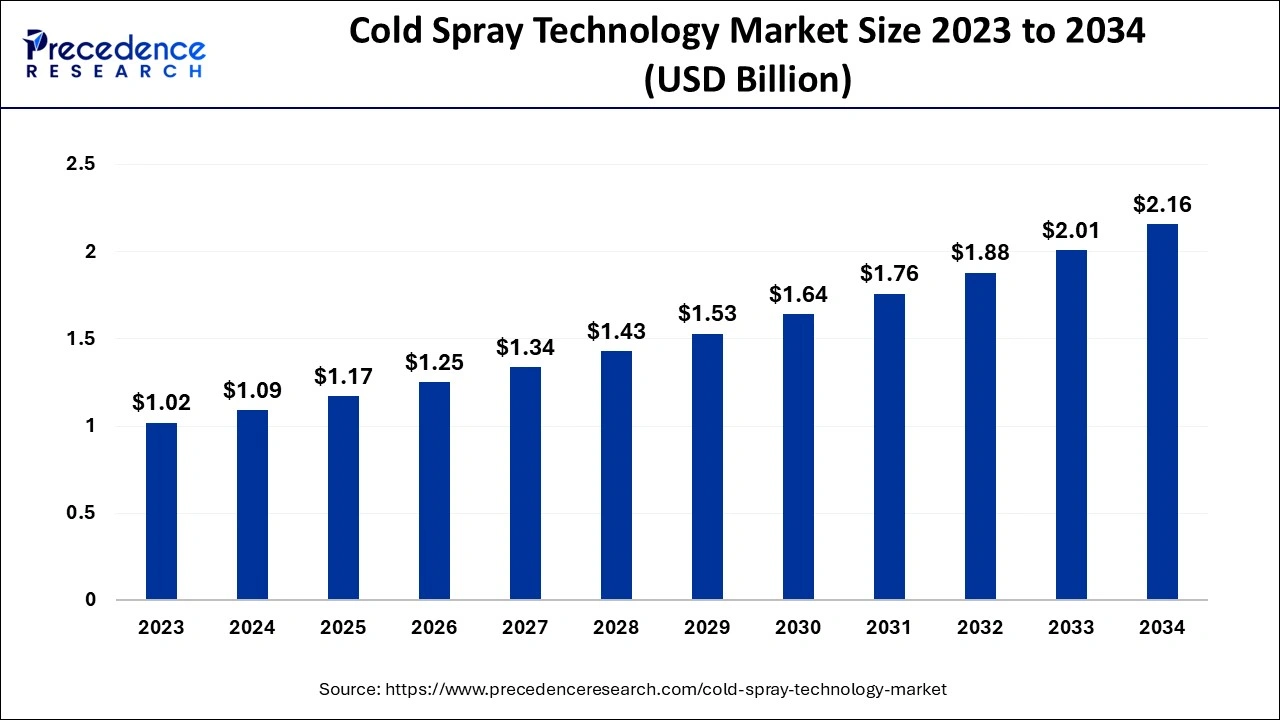
Cold Spray Technology Market Key Takeaways
- North America dominated the global market with the largest market share of 42% in 2023.
- Asia Pacific is anticipated to grow at the fastest CAGR during the forecast period.
- By material, the aluminum segment contributed the highest market share of 29% in 2023.
- By material, the titanium segment is expected to grow at the fastest CAGR over the forecast period.
- By service, the cold spray coatings segment captured the biggest market share of 90% in 2023.
- By service, the cold spray additive manufacturing (CSAM) segment is anticipated to grow at the fastest CAGR from 2024 to 2034.
- By end use, in 2023, the aerospace segment generated the major market share of 27% in 2023.
- By end use, the electrical and electronics segment is estimated to grow rapidly during the forecast period.
Cold Spray Technology Market Overview
The cold spray technology market, when analyzed by material type, includes metals such as aluminum, copper, titanium, and nickel, as well as composite materials. Cold spray is an additive manufacturing and coating process that involves the deposition of solid particles at high velocities to form a coating on a substrate without melting the particles.
The selection of material is critical in determining the application and performance characteristics of the cold-sprayed coating. Metals like aluminum and copper are widely used due to their excellent thermal and electrical conductivity, while titanium and nickel alloys are favored in aerospace and defense applications for their strength and corrosion resistance. As industries look for advanced repair, coating, and restoration technologies, the choice of material continues to play a pivotal role in shaping the market dynamics of cold spray technology.
Cold Spray Technology Market Drivers
The demand for corrosion-resistant, lightweight, and high-strength coatings is a major driver in the cold spray technology market under the material segment. Aluminum and copper remain dominant due to their suitability for protective coatings and electrical components.
Moreover, the increased use of titanium and nickel alloys in aerospace and automotive industries to reduce weight without compromising performance is pushing the demand for these materials in cold spray applications. The ability of cold spray to apply coatings without causing thermal damage also makes it ideal for temperature-sensitive materials, driving its popularity in medical, energy, and electronics industries.
Cold Spray Technology Market Opportunities
There are growing opportunities in developing new composite materials that combine the best properties of multiple metals, such as wear resistance, thermal stability, and electrical conductivity. Emerging materials tailored specifically for cold spray systems could revolutionize how industries approach component repair and enhancement.
The advancement of nanostructured powders and high-performance alloys opens new avenues for innovation. Additionally, the use of recycled or waste materials in cold spray coatings presents a sustainable path forward, aligning with global trends toward environmental responsibility.
Cold Spray Technology Market Challenges
One of the primary challenges in this segment is the limited availability of optimized powders for cold spray application. Each material requires specific particle size distributions and morphology to achieve effective bonding and coating uniformity.
The cost of high-performance materials like titanium and nickel alloys can also be prohibitive for certain industries. Moreover, ensuring consistent quality of the coating across complex geometries remains a technical hurdle, especially when dealing with advanced or composite materials.
Cold Spray Technology Market Regional Insights
North America and Europe are at the forefront of material innovation in the cold spray technology market. The presence of leading aerospace, defense, and medical industries in these regions fuels the demand for advanced materials like titanium and nickel.
Asia-Pacific, particularly China and Japan, is rapidly advancing in material science and manufacturing capabilities, expanding the use of various metals in cold spray applications. Latin America and the Middle East are emerging markets where copper and aluminum applications in oil & gas and mining industries are gaining traction.
Cold Spray Technology Market Recent Developments
Recent advancements include the development of tailored alloy powders specifically designed for cold spray application, improving bond strength and reducing porosity. Research institutions are exploring the integration of nanomaterials and hybrid composites to enhance performance.
Innovations in powder production methods, such as gas atomization and plasma-assisted synthesis, are enabling the creation of more uniform and reactive powders, optimizing deposition results.
Cold Spray Technology Market Companies
- ASB Industries (Hannecard Roller Coatings, Inc)
- Bodycote plc
- Flame Spray Technologies BV
- Plasma Giken Co., Ltd.
- VRC Metal Systems
- CenterLine (Windsor) Limited
- WWG Engineering Pte. Ltd.
- Praxair S.T. Technology, Inc.
- Impact Innovations GmbH
- Concurrent Technologies Corporation
- Effusiontech Pty Ltd (SPEE3D)
- Titomic Limited
Segments Covered in the Report
By Material
- Nickel
- Copper
- Aluminum
- Titanium
- Magnesium
- Others
By Service
- Cold Spray Additive Manufacturing
- Cold Spray Coatings
By End-Use
- Aerospace
- Automotive
- Defense
- Electrical and Electronics
- Utility
- Others
By Geography
- North America
- Asia Pacific
- Europe
- Latin America
- Middle East and Africa
Ready for more? Dive into the full experience on our website!